Understanding Valves: Types, Functions, and Their Role in Modern Industry
⬅ Back to Posts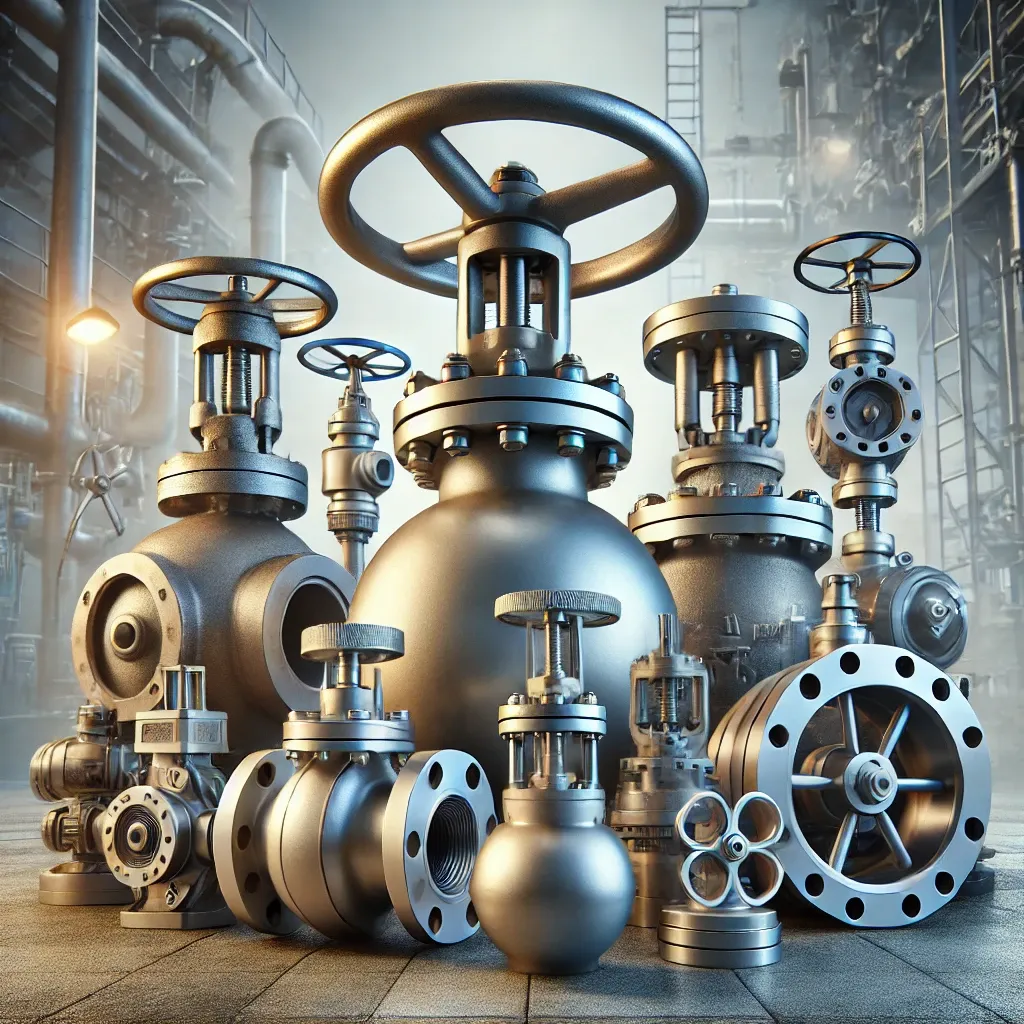
Valves are indispensable components in almost every industrial system, serving critical roles in controlling the flow and pressure of fluids, gases, and other substances. Found in applications from residential plumbing to complex oil refineries, valves ensure the safety, efficiency, and reliability of operations. This post will explore the different types of valves, their functions, and their significance across industries.
What Are Valves?
At their core, valves are devices that control the flow of fluids or gases within a pipeline or system. They achieve this by opening, closing, or partially obstructing passageways within the system. The main elements of a valve include the body, the actuator or handwheel, and an internal mechanism that moves to control flow. Depending on the type, valves can regulate fluid direction, pressure, or volume to meet specific system requirements.
Common Types of Valves and Their Functions
- Gate ValvesGate valves use a gate-like mechanism that lifts to allow flow or lowers to stop it completely. They are commonly used in applications where a full shut-off or complete flow is needed, such as in water treatment or oil pipelines. However, they are not suitable for flow throttling, as this can cause wear on the gate and lead to leakage.
- Globe ValvesGlobe valves use a plug or disc to regulate flow. By moving the disc into or out of the flow path, these valves allow for precise flow control, making them suitable for throttling applications. They are commonly found in industries requiring fine control over flow rates, such as the chemical and pharmaceutical sectors.
- Ball ValvesBall valves are characterized by their spherical disc with a hole in the center, which rotates to either allow or block flow. Known for their quick on-off action, ball valves are used in applications where tight sealing is essential, like in gas pipelines and fuel systems. They are also durable and require minimal maintenance, making them a popular choice for industrial applications.
- Butterfly ValvesThese valves use a disc that rotates around an axis to control the flow. Butterfly valves are ideal for large-volume flow control due to their compact, lightweight design and cost-effectiveness. They are frequently used in water distribution, HVAC systems, and food processing applications.
- Check ValvesCheck valves, also known as non-return valves, allow fluid to flow in only one direction. They are essential for preventing backflow, protecting equipment from potential damage caused by reverse flow. Commonly used in pumps, boilers, and sewage systems, check valves are critical for system safety and efficiency.
- Pressure Relief ValvesPressure relief valves are essential safety devices that protect systems from overpressure conditions. When the pressure within a system exceeds a predefined limit, the valve opens to release excess fluid or gas, preventing potential equipment damage or failure. These valves are used in applications like steam systems, oil refineries, and chemical processing plants.
Key Functions of Valves in Industrial Systems
- Flow ControlValves control the volume of fluid or gas that passes through a system, allowing for precise regulation in various applications. Whether it's controlling water flow in a municipal water supply or regulating fuel in a combustion system, valves ensure that flow rates are optimized.
- Pressure RegulationValves can maintain pressure levels within safe limits, which is especially critical in high-pressure systems. By adjusting or releasing pressure, valves protect equipment from overpressure and ensure system stability.
- System IsolationIsolation is essential during maintenance, repairs, or emergency shutdowns. By shutting off specific sections, isolation valves prevent fluid or gas from reaching certain areas, allowing for safe intervention without affecting the rest of the system.
- Preventing BackflowBackflow can lead to contamination, equipment damage, and inefficient operation. Valves like check valves prevent this by allowing flow in only one direction, which is especially important in sensitive systems such as water treatment facilities and food processing.
Choosing the Right Valve for Your Application
Selecting the appropriate valve type depends on several factors, including:
- Nature of the Fluid or GasThe type of substance flowing through the valve affects its material choice and construction. For example, corrosive fluids require materials resistant to chemical reactions, such as stainless steel or specific alloys.
- Operating Pressure and TemperatureValves must withstand the system’s operating conditions without failure. For high-pressure applications, such as oil and gas pipelines, durable valves made from high-strength materials are essential.
- Flow Control RequirementsSome applications require precise flow control, while others only need on-off control. For example, globe valves are excellent for throttling, while ball valves are better suited for simple shut-off functions.
- Maintenance NeedsSome industries, such as food and beverage, require frequent cleaning and maintenance, making easy-to-maintain valves a priority. Similarly, in remote locations, low-maintenance valves reduce downtime and ensure reliable operation.
- Cost EfficiencyWhile some valve types, like ball valves, are more expensive, their longevity and low maintenance often justify the initial cost. For large-scale applications where budget constraints exist, butterfly valves are often chosen for their cost-effectiveness and ease of installation.
The Importance of Valves Across Industries
Valves play a vital role in virtually every industry:
- Water Treatment and Distribution: Valves control water flow and pressure throughout the distribution network, ensuring consistent water supply to residential, commercial, and industrial areas.
- Oil and Gas: Valves regulate the flow of crude oil, gas, and refined products in pipelines, ensuring safe and efficient transport from extraction points to refineries and distribution centers.
- Chemical Processing: Valves are used to control the flow of chemicals and gases, ensuring safety, process accuracy, and compliance with environmental regulations.
- Food and Beverage: Sanitary valves ensure the safe processing and transport of food and beverage products, preventing contamination and maintaining product quality.
- HVAC: Valves in heating, ventilation, and air conditioning systems control the flow of air, water, and refrigerants, ensuring efficient climate control and energy use.
Future Trends in Valve Technology
- Automation and Smart ValvesWith advancements in technology, smart valves equipped with sensors, actuators, and IoT capabilities are transforming the valve industry. These valves provide real-time data on flow rates, pressure, and temperature, allowing for predictive maintenance and automated system adjustments.
- Sustainable Materials and DesignsEnvironmentally friendly materials and designs are gaining traction, driven by the need to minimize environmental impact. Valves that reduce energy consumption or are made from sustainable materials are becoming more popular, particularly in industries with strict sustainability goals.
- Increased Focus on Safety and ComplianceAs industries face tighter regulatory scrutiny, valves with built-in safety features and compliance certifications are becoming standard. This focus ensures that valves meet international safety and quality standards, providing greater reliability and safety.
- Customization and Specialized ApplicationsAs industries demand more specialized solutions, manufacturers are increasingly offering customizable valves that cater to unique applications. This trend is especially prevalent in sectors such as biotechnology, pharmaceuticals, and high-precision manufacturing.
Valves are indispensable for safe and efficient operation across industries. From managing water supplies to regulating the flow of hazardous materials, valves ensure system reliability, safety, and performance. As technology advances, valves are evolving with innovations like smart automation and sustainable designs, enhancing their functionality and reducing operational risks. Choosing the right valve type and understanding its application are essential for optimising performance, safety, and efficiency.