Understanding Ultrasonic Level Sensors
⬅ Back to Posts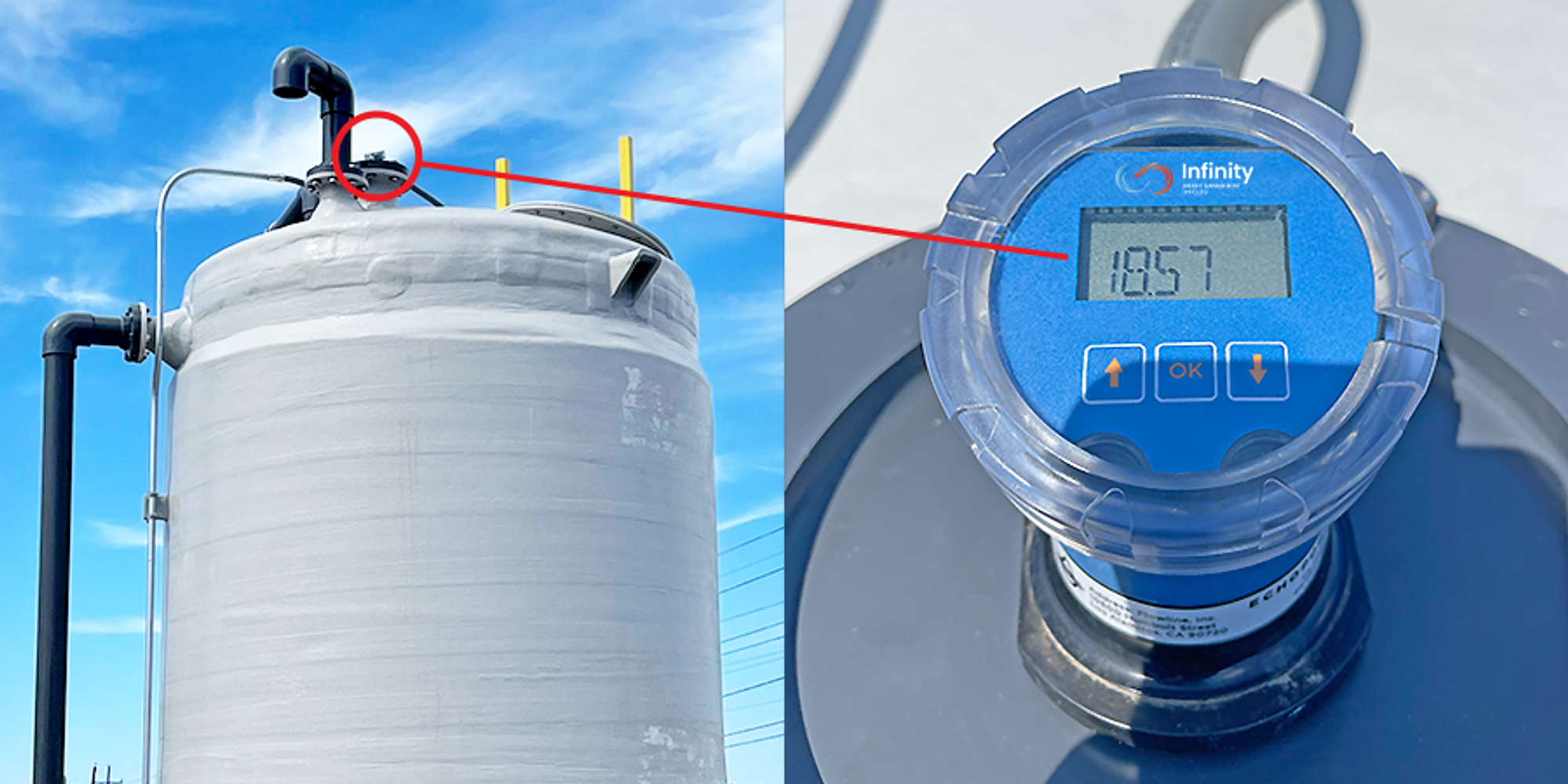
Ultrasonic level sensors are devices used to measure the level of liquids or solids within a container, tank, or open channel. They are widely used in various industries, including water and wastewater management, chemical processing, food and beverage, and manufacturing, due to their non-contact measurement method, reliability, and versatility.
How do Ultrasonic Level Sensors Work?
Ultrasonic level sensors operate by emitting ultrasonic sound waves from a transducer. These sound waves travel through the air, bounce off the surface of the liquid or solid being measured, and then return to the sensor. The sensor measures the time it takes for the sound waves to travel to the surface and back, known as the "time of flight."
By knowing the speed of sound in air and the time of flight, the sensor calculates the distance from the transducer to the surface of the material. This distance measurement is then used to determine the level of the material within the tank or container. The level can be calculated as either the distance from the sensor to the material surface or, inversely, the height of the material above the container bottom. Ultrasonic level sensors can be configured to provide continuous level measurements or to trigger alarms at specific levels, depending on the application requirements.
Key Advantages
Non-Contact Measurement: One of the primary advantages of ultrasonic level sensors is their non-contact measurement method. The sensor does not need to touch the material being measured, which is ideal for measuring corrosive, hazardous, or hygienic materials where contamination and wear are concerns.
Versatility: Ultrasonic level sensors can measure the level of both liquids and solids in a wide variety of applications, from water and chemicals to grains and powders. This versatility makes them suitable for a broad range of industries.
Low Maintenance: With no moving parts, ultrasonic level sensors are generally low-maintenance devices. They are resistant to wear and tear and have a long operational life, reducing downtime and maintenance costs.
Easy Installation: Ultrasonic sensors are relatively easy to install and can be mounted at the top of tanks, containers, or open channels. They do not require complex wiring or extensive setup, making them a cost-effective solution for level measurement.
Applications
Water and Wastewater Management: Ultrasonic level sensors are commonly used in water treatment plants and wastewater facilities to monitor tank levels, open channel flow, and sump levels, helping to manage resources efficiently and prevent overflows.
Chemical Processing: In the chemical industry, these sensors measure the levels of various liquids and chemicals, ensuring safe storage and accurate inventory management.
Food and Beverage: Ultrasonic sensors are used to measure the level of liquids and solids in storage tanks and silos, maintaining accurate inventory and ensuring consistent product quality.
Manufacturing: They are employed in various manufacturing processes to monitor the levels of raw materials and finished products, optimising production and reducing waste.
Challenges and Considerations
While ultrasonic level sensors offer many advantages, there are some challenges and considerations to be aware of. The accuracy of these sensors can be affected by environmental factors such as temperature, humidity, and the presence of dust or foam on the material's surface. Extreme temperatures can alter the speed of sound in air, affecting the accuracy of level measurements. Additionally, ultrasonic waves may struggle to penetrate foam, which can result in false readings or reduced accuracy.
Another consideration is the sensor's blind zone, which is the minimum distance from the transducer to the material surface that the sensor can accurately measure. If the material level falls within this blind zone, the sensor may not provide reliable data, necessitating careful placement of the sensor to ensure accurate measurements.
Ultrasonic level sensors are an effective and versatile solution for level measurement across a variety of industries. Their non-contact measurement method, ease of installation, and low maintenance requirements make them a preferred choice for applications where reliability and simplicity are key. While environmental factors and installation considerations must be taken into account, the benefits of ultrasonic level sensors often outweigh these challenges, making them an essential tool for managing liquid and solid levels in industrial processes.