Understanding Metal Tube Rotameters: How They Work and Where They Shine
⬅ Back to Posts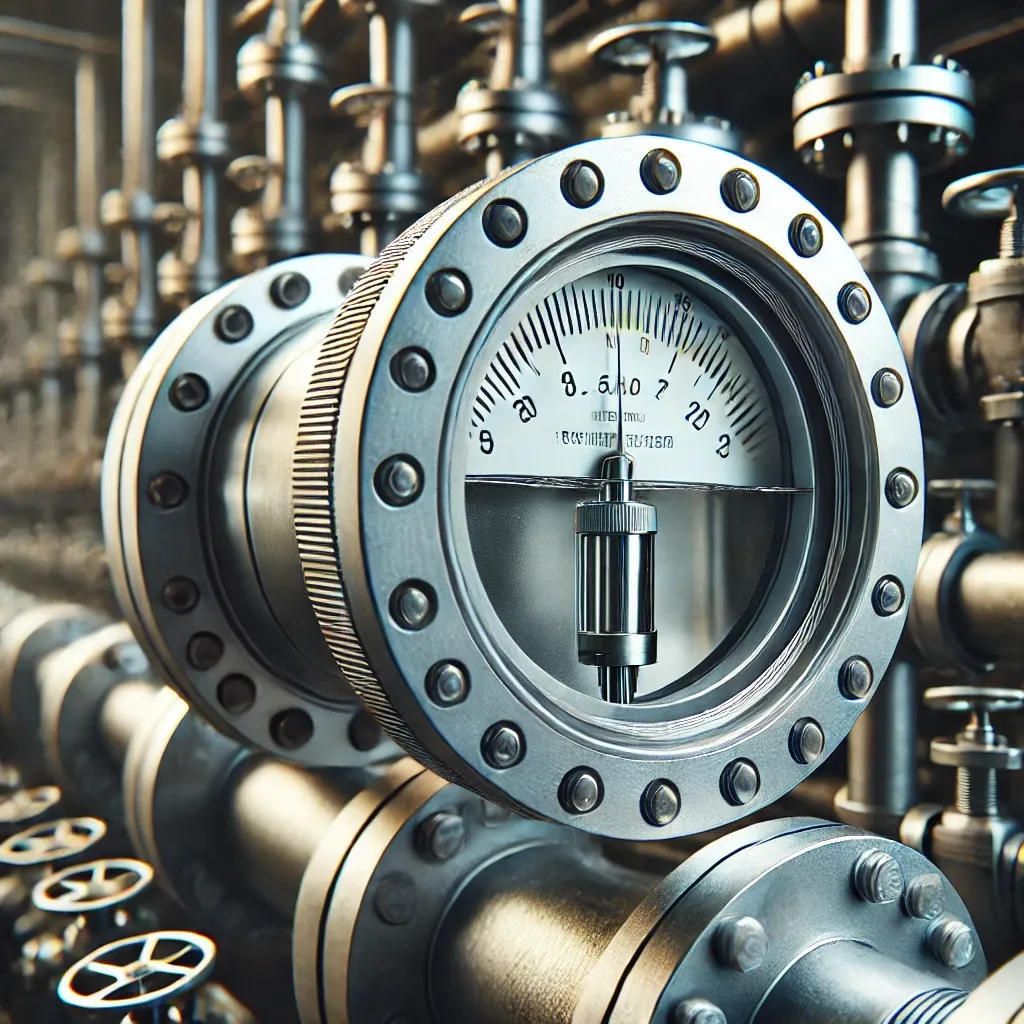
A metal tube rotameter is a versatile flow measurement device commonly used in industrial settings. Known for its rugged construction, reliability, and straightforward operation, the metal tube rotameter is ideal for applications where durability is a priority, especially in environments with high pressure, temperature, or corrosive fluids. In this article, we’ll explore how metal tube rotameters work, their advantages, and their common applications.
What is a Metal Tube Rotameter?
A metal tube rotameter is a type of variable area flow meter. Unlike traditional glass-tube rotameters, it uses a metal tube with a float inside to measure the flow of liquids or gases. The metal tube design offers added protection and durability, making it suitable for industrial environments where traditional glass rotameters might not be suitable.
In a metal tube rotameter, the fluid flows upward through a tapered metal tube that contains a float. As the flow increases, it pushes the float higher up the tube, allowing for a quick and visual reading of the flow rate.
How Metal Tube Rotameters Work
The working principle of a metal tube rotameter is based on variable area flow measurement. Here’s a closer look at the process:
- Fluid Flow and Float Lift: As the fluid flows upward through the tube, it exerts force on the float inside the tube, causing it to rise.
- Balancing Forces: The float rises until the upward force exerted by the fluid flow balances with the downward force of gravity. The point where these forces equalize depends on the flow rate of the fluid.
- Flow Measurement: Since the tube is tapered (wider at the top), the area between the tube and the float increases as the float rises. At any given height, the float's position corresponds to a specific flow rate, which can be read on a scale or transmitted to a display.
Key Components of a Metal Tube Rotameter
- Tapered Metal Tube: The tube is typically made of stainless steel or other corrosion-resistant metals to withstand high pressures and temperatures. Its internal diameter gradually widens from bottom to top, creating the variable area needed for measurement.
- Float: The float, usually made from a dense material like stainless steel, sits inside the tube. It is lifted by the fluid flow and reaches an equilibrium height based on the flow rate.
- Scale: Most metal tube rotameters come with a scale that directly displays the flow rate, allowing for easy reading without complex calculations. For remote monitoring, some models can transmit the flow rate data electronically.
- Magnetic or Transmitter Systems: Some metal tube rotameters use magnetic floats and transmitters to provide output signals to remote devices. This is particularly useful for industrial applications where real-time flow data is essential for process control.
Advantages of Metal Tube Rotameters
Metal tube rotameters are especially popular in industrial settings due to their numerous advantages:
- Durability: The metal construction makes them highly resistant to damage from impact, high pressure, and temperature variations. This durability is essential in heavy-duty applications where equipment is subjected to harsh conditions.
- Corrosion Resistance: Metal tube rotameters can handle corrosive fluids, especially when made from corrosion-resistant materials like stainless steel or coated with protective layers.
- High Pressure and Temperature Handling: The design allows these rotameters to operate in environments with high pressures and temperatures, where traditional glass-tube rotameters might fail.
- Simple, Visual Flow Indication: Metal tube rotameters provide a clear and direct indication of flow rate, making them easy to read and operate without complex electronics.
- No External Power Requirement: Many metal tube rotameters operate purely mechanically, requiring no external power source, making them suitable for remote or hazardous locations.
Limitations of Metal Tube Rotameters
While they are incredibly useful in many applications, metal tube rotameters do have some limitations:
- Limited to Vertical Installation: Metal tube rotameters must typically be installed vertically, with fluid flowing upward. This limitation can restrict their use in certain pipeline configurations.
- Less Accurate at Very Low Flow Rates: Rotameters generally struggle with low flow rates, where even small variations can affect the float position and reading accuracy.
- Dependence on Gravity: Since the operation relies on gravity, rotameters are not suitable for zero-gravity or microgravity environments, making them less versatile than some other flow meter types.
Applications of Metal Tube Rotameters
Thanks to their robustness and accuracy, metal tube rotameters find use across various industries. Here are some common applications:
- Chemical Processing: Metal tube rotameters are ideal for measuring the flow of chemicals and gases in the chemical processing industry, where corrosive and high-pressure fluids are common.
- Oil and Gas: In the oil and gas sector, these rotameters measure the flow of various gases, oils, and fluids, often in high-pressure and high-temperature conditions.
- Water Treatment: Metal tube rotameters are used in water and wastewater treatment plants for flow measurement and monitoring.
- Food and Beverage: These rotameters can handle the demands of the food and beverage industry, measuring flow in processes like ingredient dosing and waste management.
- Pharmaceuticals: In pharmaceutical manufacturing, metal tube rotameters provide accurate flow measurements for mixing and dosing processes.
Choosing the Right Metal Tube Rotameter
When selecting a metal tube rotameter, it’s essential to consider factors such as:
- Material Compatibility: Ensure the rotameter material is compatible with the fluid being measured to prevent corrosion or chemical reactions.
- Pressure and Temperature Requirements: Choose a rotameter rated for the specific pressure and temperature ranges of your application to avoid performance issues.
- Flow Rate Range: Make sure the rotameter’s measurement range matches your required flow rates, especially if measuring low or fluctuating flows.
- Output Requirements: If remote monitoring is needed, look for a model with an electronic transmitter or magnetic float that can provide output signals for data logging and control systems.
Metal tube rotameters are an excellent choice for flow measurement in industrial applications where durability, reliability, and straightforward operation are paramount. Their ability to handle challenging environments and provide accurate, real-time measurements makes them invaluable in sectors like chemical processing, oil and gas, and water treatment. Although they have limitations, such as limited accuracy at low flow rates and a dependence on vertical installation, their robust construction and simplicity often outweigh these drawbacks. When chosen and installed correctly, a metal tube rotameter can be a highly effective tool for reliable flow measurement in demanding conditions.